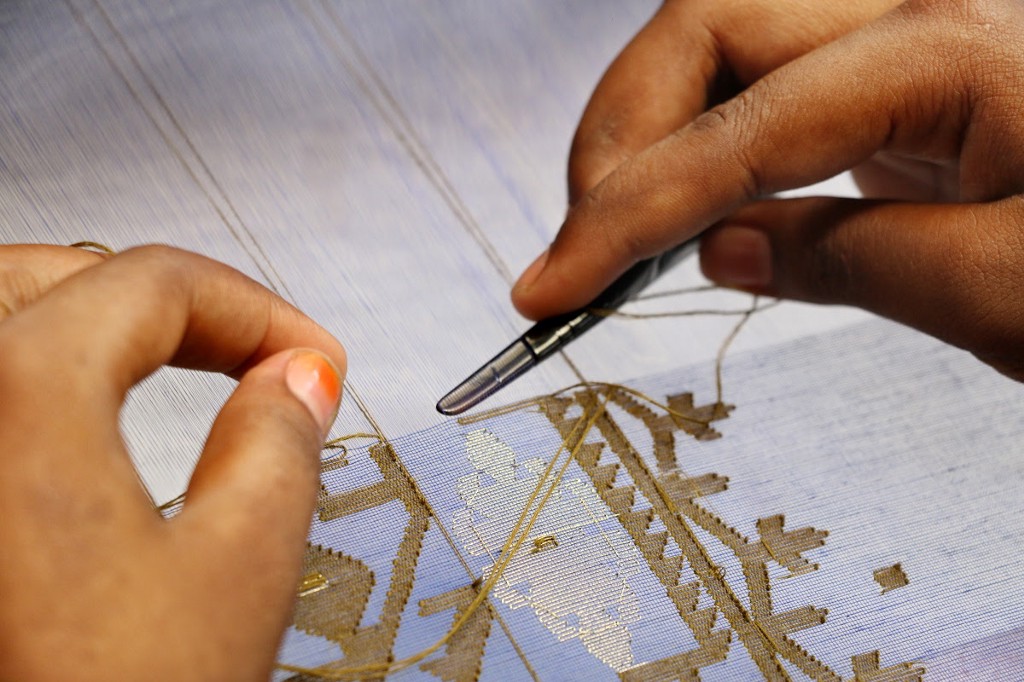
The art of weaving is exactly that — an art. It requires skill, precision and rhythm, which when repeated over and over, produces a delicate weave. Jamdani weaves, however, require more than this. Since the defining aspect of this textile are its rich motifs, which are all intricately added by hand, Jamdani is touted as the most advanced hand-weaving technique in the world. Each motif has to be inlaid into the fabric by adding denser threads to fine warp threads, and this process is so time-intensive that on a usual day, an artisan can weave only between a quarter and one inch of fabric. That shockingly translates to a year if we’re looking at a handwoven Jamdani sari. No wonder the traditional art of weaving Jamdani was declared a UNESCO Intangible Cultural Heritage of Humanity in 2013. Let us understand the nuances of weaving this fabled fabric.
Jamdani is One of the oldest weaving traditions of India , which dates back to almost 2000 years old. They are also known as Dhakai Jamdani, for their original place of origin was Dhaka in Bangladesh. These sarees are highly ornate handwoven drapes. They are labour intensive and involve complex weaving process. These sarees are known for the usage of the finest Muslin fabric, which lends a transparent body to the saree. The motifs woven on them appear like they are floating on thin air. Jamdani sarees were heavily patronized by the Moghuls, whose influences are evident on the design of these sarees. The birth of Jamdani however is unclear, but it enjoyed patronage from Jehangir, an artist himself. It was during this period when the Bengal region, one of the richest provinces of Mughal Empire, became a hub for Jamdani’s weaving industry. Jehangir’s patronage elevated Jamdani to a status of royalty and a sign of luxury, and was much admired by visiting European dignitaries and ambassadors who were enamoured by its intricacies and quality.
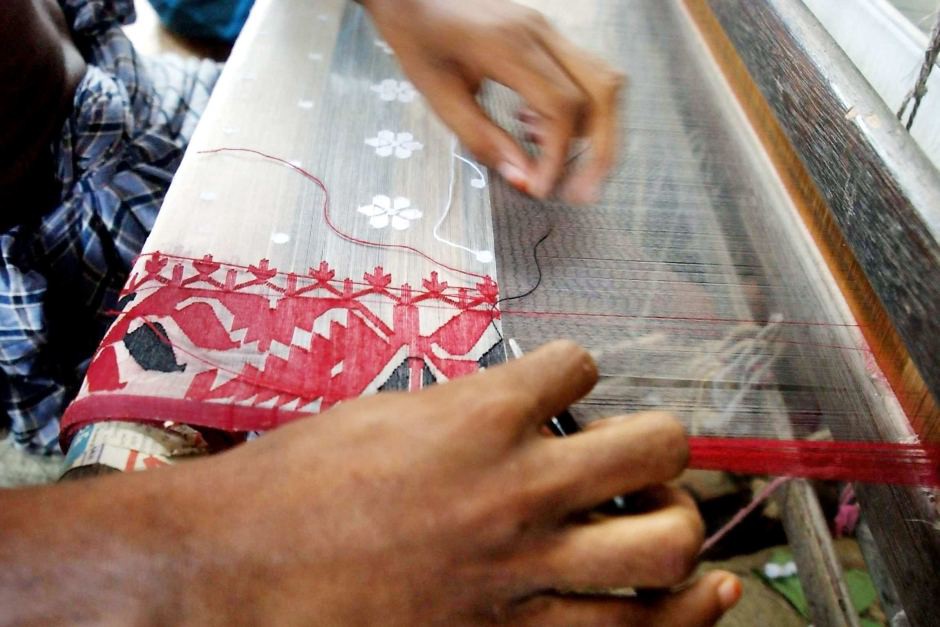
Descent and Decline
“Just like the empire itself, the industry gradually fell into disdain. “
By the mid-eighteenth century, Jamdani along with other genteel fabrics saw a rapid decline. With the Mughals plagued by infighting and political turmoil, Jamdani lost its strongest benefactors it was ordained with.
With the advent of mills in Manchester and rise of colonial powers in the subcontinent, Jamdani fell behind its power loom competitors as it required strenuous labor and copious amounts of money to keep the industry running. By the end of 19th century, the industry was all but lost in oblivion and the once bustling and fabled mills of Dhaka fell into disuse and neglect.
Sulaiman, a 9th-century Arab traveller, wrote of cotton fabrics made in the kingdom of Rahmi (erstwhile undivided Bengal) which were so fine they could pass through a signet ring. Around the 12th century, Islamic influences infused the fabric with countless motifs and colours. And through the magic of one inlaid thread — added discontinuously onto the loom — it turned into a surface for mesmerising patterns. The technique created motif-rich fabrics that bore poetic names like Shabnam (morning dew), Ab-i-rawan (flowing water) and Baftnama (woven wind). It was during the Mughal emperor Akbar’s reign that the art blossomed into its most exquisite form — the flowered muslin, Jamdani.
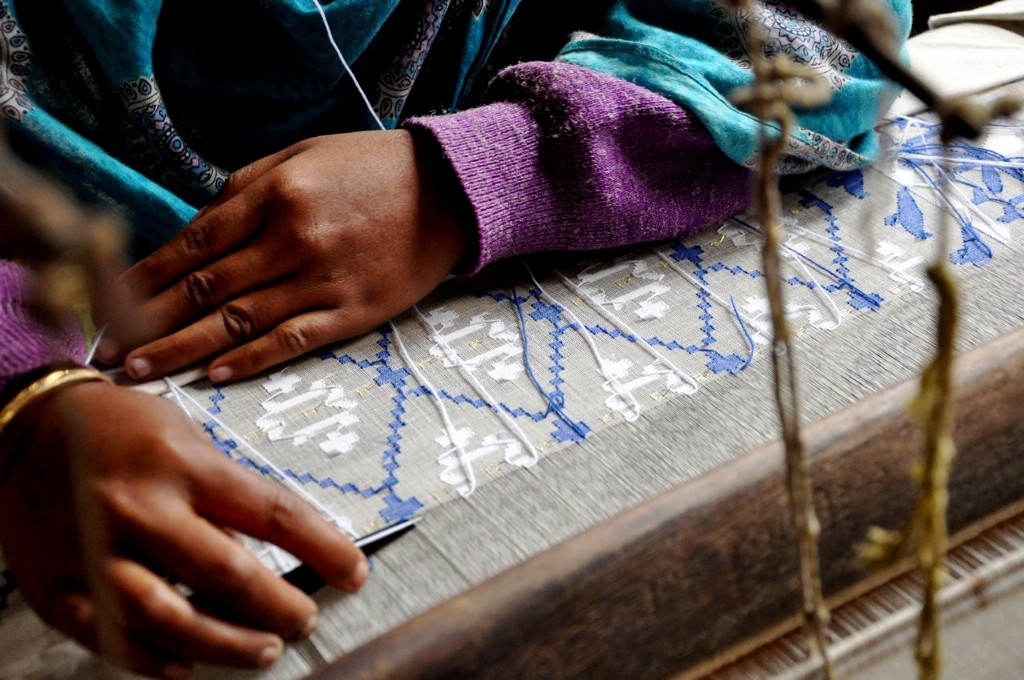
Jamdani is a discontinuous weft technique of weaving, and can be defined as the art of fine ‘Parsi Gara’ done on the loom. In Jamdani, motifs are inlaid into the fabric by adding a denser thread to fine warp threads by hand. This process is considered the most time intensive and one of the most advanced hand weaving techniques in the world.
Jamdani weaving is like tapestry work where small shuttles of coloured, gold or silver threads pass through the weft. Designs range from the “butidar” (wherein the entire sari is dispersed with florals), the “tercha” (diagonally striped florals), or “jhalar” (a network of floral motifs).
Originally, the base for the Jamdani technique was muslin — the finest cloth ever woven by human hand. It shares its lineage with several ethereal muslin fabrics of India, which were lost when the erstwhile East India Company began its systematic destruction of India’s textile industry in the late 18th century.
A matchless interweave of age-old tradition and constant revival, Jamdani — the flower vase — survives as a living relic of a glorious legacy. It is a celebration of beauty passed on to us, despite all odds, by those who came before.
A Jamdani weaver can have between 100 and 300 different discontinuous weft threads laid out before her as she weaves. She picks the right thread and interweaves each weft by hand through thousands of warp threads. On a usual day, an artisan weaves between a quarter and one inch of fabric. This means a weaver could spend more than a year weaving one Jamdani sari. Largely, it depends on the intricacy and density of the design. That said, a sari takes anywhere between six months to three years to weave, where a pair of weavers weave for 10 hours a day.
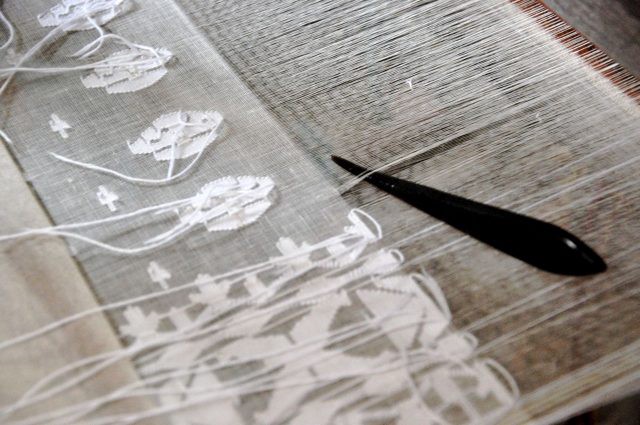
Jamdani sarees are known for their intricate designs and their supreme quality fabrics. They speak of luxury and royalty with their unparalleled beauty. Authentic Jamdani sarees takes more than a few hundred hours to weave just one piece, making theme exclusive to the elite class. However, the advent of advanced mills made the process must easy and are now available at a much lower cost. These sarees are highly treasured by the Bengali women, whose wardrobe is considered incomplete without this variety.
The making of jamdani starts way before the weaving starts .The Threads for weaving are first sized before weaving the fabric .Sizing can be done by machine or hand. Starch is often used as sizing for cotton warp yarns. Rice is used as the starch sizing medium in Burdwan. A special variety of rice — Kolma or Dohar Nagra — is preferable for this. Rice and the popped version made from the same, called khoi, are essential for the sizing mixture.
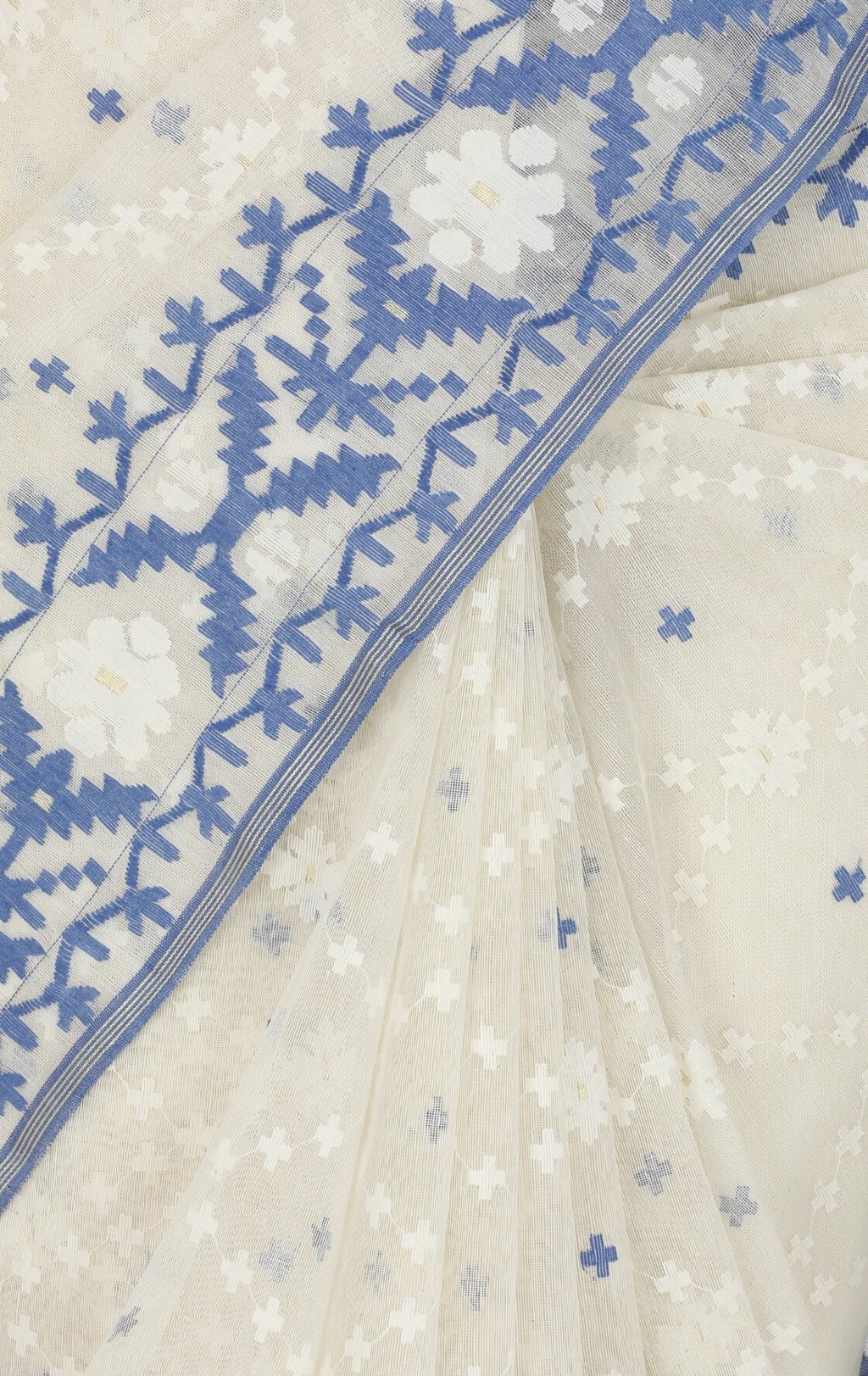
The cooked rice ‘bhaat’ and popped rice have to be converted into a starch strong enough to hold through the infinite movements that go into weaving the fabric. There are precise measures of how much cooked rice must be added to previously soaked popped rice and mixed together with the starchy water produced by rice as it cooks.
One needs to know exactly when the starch, cooked and soaked popped rice can be mixed. They cannot just be mixed when the ingredients are ready but when the moisture in the air and temperature are just right — at four in the morning. A large high edged stone platter is taken and the khoi-bhaat mixture is combined with the tamarind-rice starch water. The mixture is then kneaded into the cotton strands deftly, ensuring that there is not a drop of excess moisture in the strands,. This is done for about twenty five minutes or so by which time the entire mixture is absorbed by the yarn.
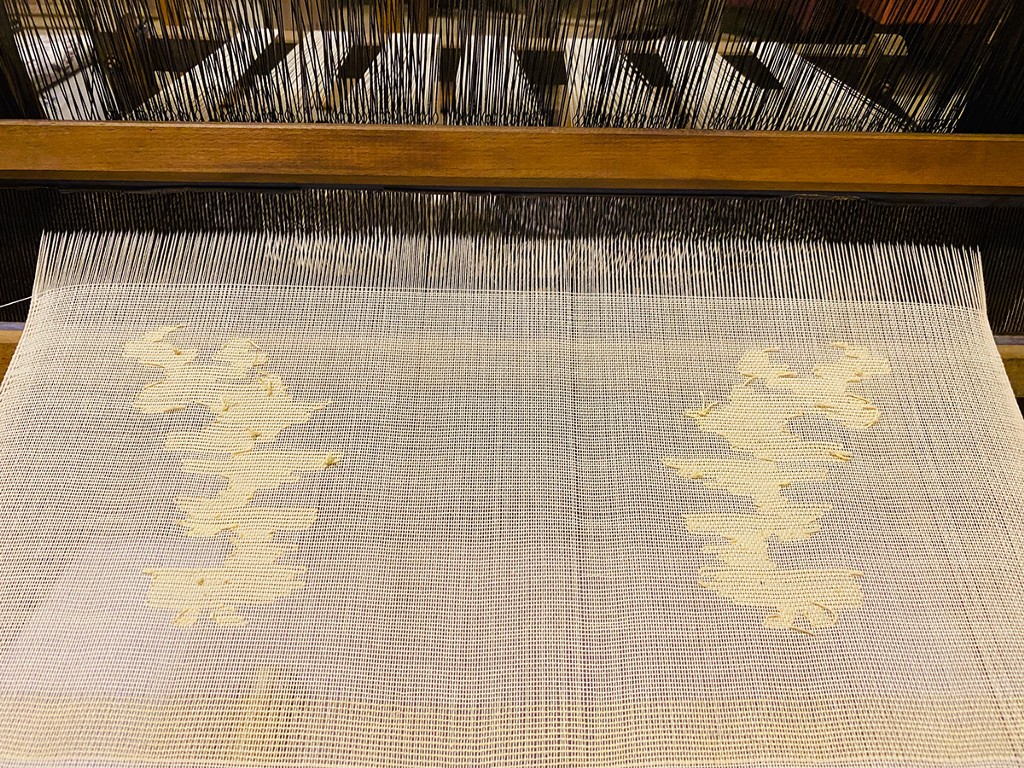
When Jamdani began in Dhaka, the motifs were nature inspired but geometric in shape. The weavers created these motifs by counting threads instead of any machinery. Hence, the geometric nature of the motifs. The Jamdani in Uppada was done with a jala (threads to pick up the warp) and saw small buttis which weren’t intricate.
In Jamdani weaving the paper design is kept under the warp and the weaver replicates the design. The paper Jamdani gives boundless opportunities for experimentation and the liberty to design anything. For the weaver, it gives him the capability to weave wide-ranging design. Therefore, the Jamdani pattern of weaving is considered to be one of the most advanced styles of weaving. These sarees also feature pure gold and silver laces (zari) to boost the splendor of the outfit. The interweaving of threads, looming, adding the knots and preparing the border is a tiresome process and requires immense skill which makes the saree even more magnificent. Great skill goes behind weaving each Jamdani Saree as a thick weft is added depending on the design along with a thin one. This makes the design synonymous with both sides of the saree. This weaving pattern is laborious and time taking and therefore it makes the saree precious and the production volume low.
Features Of Jamdani Sarees:
Here are some of the noteworthy features of a Jamdani saree:
- Jamdani sarees reflect the Persian and Mughul influences in their motifs.
- The word Jamdani literally translates to “Jam” means flower and “dani” means vase.
- Common motifs used are florals, Bel leaves and other geometric patterns.
- These sarees make use of silver and gold Zaris for extra richness.
- The original colors used in Jamdani sarees were grey and red. However, many colors are now made available in this variety.
· The earliest mention of the origin of Jamdani and its development as an industry is found in Kautilya’s book of economics (about 300 AD) where it is stated that this fine cloth used to be made in Bengal and Pundra. Its mention is also found in the book of Periplus of the Eritrean Sea and in the accounts of Arab, Chinese and Italian travelers and traders. Four kinds of fine cloth used to be made in Bengal and Pundra in those days, viz khouma, dukul, pattrorna and karpasi. From various historical accounts, folklore and slokas, it may be assumed that very fine fabrics were available in Bengal as far back as the first decade before Christ. Cotton fabrics like dukul and muslin did not develop in a day. Dukul textile appears to have evolved into muslin. Jamdani designs and muslin developed simultaneously. The fine fabric that used to be made at Mosul in Iraq was called mosuli or mosulin In his 9th century book Sril Silat-ut-Tawarikh the Arab geographer Solaiman mentions the fine fabric produced in a state called Rumy, which according to many, is the old name of the territory now known as Bangladesh. In the 14th century, Ibn Batuta profusely praised the quality of cotton textiles of Sonargaon. Towards the end of the 16th century the English traveler Ralph Fitch and historian Abul Fazl also praised the muslin made at Sonargaon.
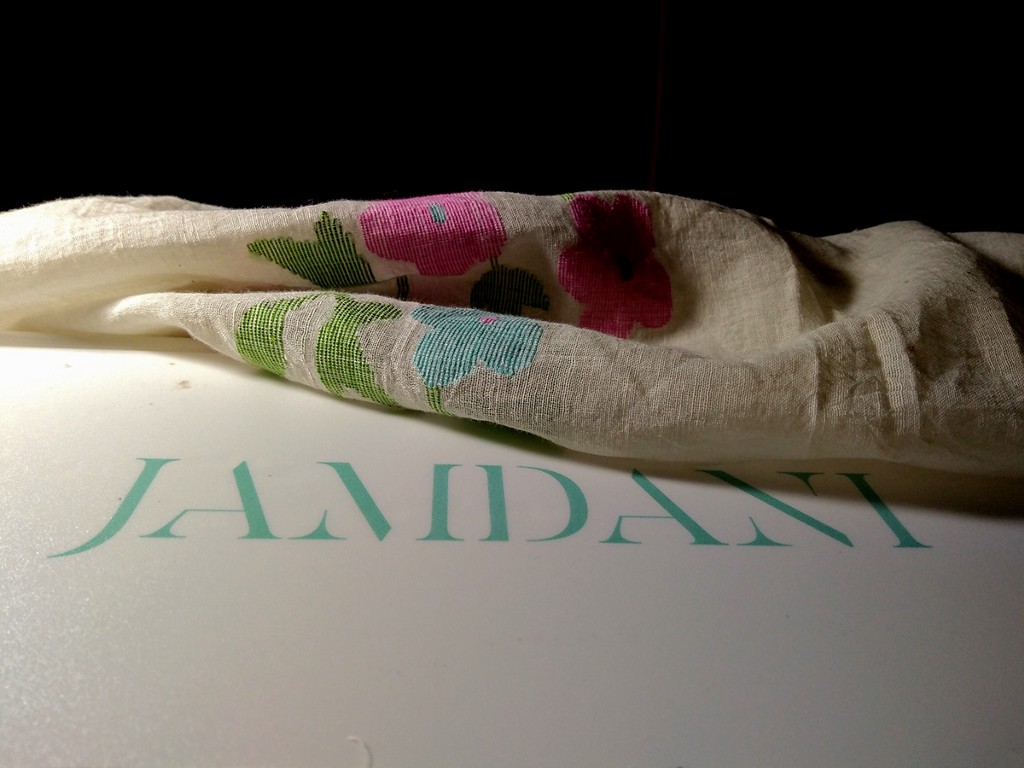
· The delicate muslins of ancient Dhaka were used for both male and female attaire in the Moghul court and the province of Bengal flourished both in commercial trade and agriculture at this time. In 1628 we find the writings of Italian traveller Manrique, which describes the patronage of the court of Emperor Shahajahan, and later Emperor Aurangzeb, who received annual tributes of these fine cloths from their governors in Bengal and which were so special as to cost ten times the price of any other cloths made for Europeans or others in the Empire.
· We are further informed that Muslim merchants in 1887 protested against the monopoly of the East India Company’s hold on weaver’s throughout East Bengal (48, 000 persons), which was done by issuing permits which prevented the weavers from taking on work from private traders. The entry of Muslim immigrant-travelers and traders proceeded the of Islam (11th century AD) to the subcontinent by at least a hundred years. Even though it was not till the early 1200s AD that Muslim conquerors settled in Bengal, contact with Arab traders, and Persian and Turkish religious mendicants had already taken place via the coastal ports in the Bay of Bengal and through the northern western land route.
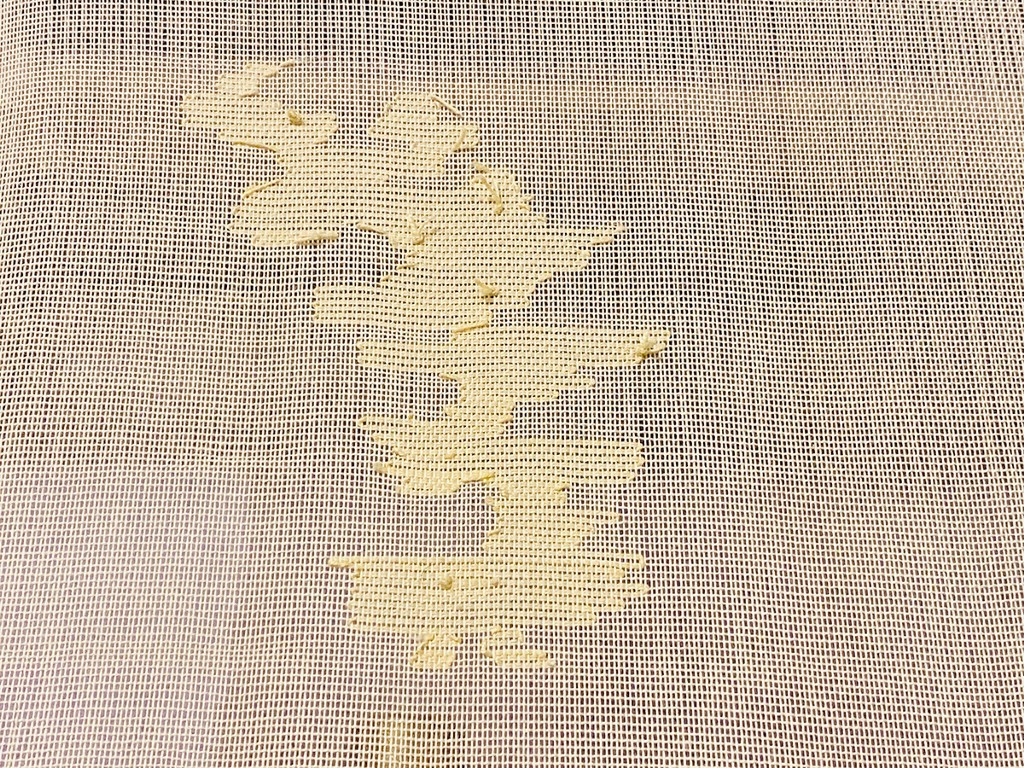
·Muslim rule which commenced in Bengal in 1268 with the reign of the Tughlaks, the area of western Bengal then called Lakhnauti, and in the eastern part called Bangalas was receptive to the message of Islam which spoke of social equality. By the time of the first independent Sultan Shams-uddin Ilyas Shah in 1342 an area considered to be a Sultanate was declared, although it did not constitute the entire region of Bengal as we know it after the British held their sway. The excellence of cotton mulmul or muslin produced on the Dhaka loom was raised to an art par excellence by Moghul patronage, and achieved a uniqueness which has remained unparelled among handloom cloth all over the world. When woven for royalty the muslin was called Mulmal Khas (king’s special) and the viceroys who placed orders for the Emperor gave it poetic names such as Ab-e-rawan (running water), Shabnam (evening dew) and Sharbati (winelike). The pinnacle of perfection came in the evolution of a special weave with motifs ‘embroidered’ along the weft and this fabric was named ‘jamdani’ which became renowned as the figured or flowered muslins. Dhaka jamdani, more than any other woven craft, became synonymous with Muslim weaving skills. The origin of the word Jamdani has no substantiated etymological explanation, but it is a Indo-Persian word and in its strictest meaning describes ‘jama’ or clothing.
EXTRA WEFT PATTERNING
The dominant feature of jamdani is its exquisite design element, woven into perfection into the gauzy fabric. Although sometimes mistaken for embroidery, jmamdani is not embroidered, but rather figured on the loom. Jamdanis are woven in plain weave, the simplest form of interlacing with supplementary extra weft. The cloth structure is very balanced and strong due to the plain weave interlacing.
Previously jamdani was woven by two weavers: the master weaver (ostad) and the assistant (shagird). The former used to call out the buli, verbal instructions for the motifs to be woven, to the latter who used to follow it with care.

Now the jamdani weaving is done by one weaver only. The buli or sloka has been memorized by the weaver or else paper patterns of the design are laid under the warp thread and followed to the last detail. In some cases, the design is traced onto the warp. A long needle like tool is used for the extra weft patterning.
Pattern Layouts
There are a few basic layouts of floral and linear designs. Individual floral motifs or sprigs scattered over the surface are called butidar. In butidar layouts the forms are not connected. The motifs are repeated in a straight or half stepped repeat. The floral sprays when arranged diagonally are known as terchi. These designs in particular are difficult to work on the loom. In some terchi layouts the designs go in a zig zag formation and change direction.
When these motifs create a network of patterns covering the entire ground they are referred to as jhalar or jaal. These are usually all over patterns. The body pattering in this sari is an ogival jaal.

Colours
Traditionally, jamdani was essentially white, off-white or grey in colour. The design appeared like a shadow on the muslin. There was a wide range of jamdanis in whites, off-whites with permutations between unbleached undyed, half-bleached and white.
It can be said that the simple paletters were based on the natural colors of the fibres used. Even when colour was used, it was in a manner that crated contrasting monochromatic designs most often in red, black or blue against a white or natural coloured background. During its heydays, the extra weft yarns were dyed with vegetable colour”; from the juice of the palash flower, fruits like plums and pomegranates, berries and indigo. Nowadays, mostly chemical dyes are used. Over a period of time, the traditional colour palette has been added to, and today jamdanis of all colours are available. “In terms of colour and design, contemporary jamdanis fall into six categories: those with
1. Natural-coloured, unbleached cotton grounds with bleached white cotton supplementary work.
2. Pastel-coloured grounds with white supplementary work.
3. Dark-coloured grounds (usually black, dark blue, dark red) with white supplementary threads.
4. Any of above, with coloured threads, either of similar or contrasting tones.
5. Any of the above combinations with zari supplementary threads as part of the mix.
6. Dark grounds with only zari supplementary work.
Neelambari
The neelambari is the best known among the colored jamdanis. It has an indigo body ornamented with silver / gold or madder red that comes up strikingly against the dark base. It is known to have been worn in Bengal for the devi puja or Kartik Amavasya, the moonless night during Navatri, coinciding with Diwali, the festival of lights, a celebration of the Goddess in her most benign and enigmatic form.
Traditional Motifs
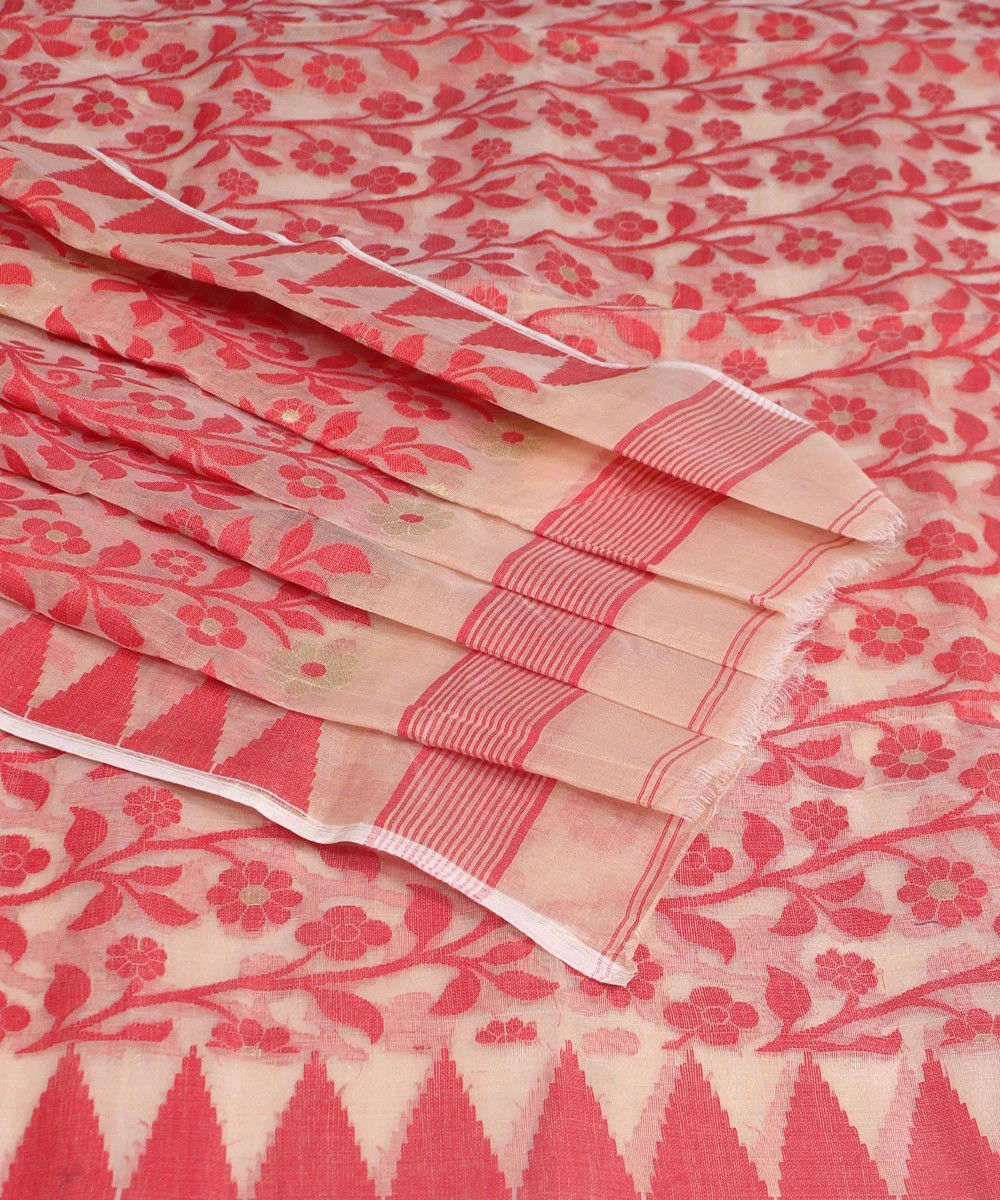
Over the years jamdani designs have taken on the indigenous names drawn from images surrounding the weavers world. Most jamdani weavers in olden days were Muslim and were forbidden by their religion to depict human form. They took inspiration from nature and the elements. The motifs reflect their own depiction and representation of everyday objects from their environment, especially plants: petals, buds, flowers and creepers. .
Some of the names of the more elaborate designs and motifs are as follows: pati (petal), angti (ring), baghnoli or bagher paa (tiger claws or paws), shankha (shell), dubla (grass), phool (flower), shapla (lotus), sabudana (barley), kori (bud), chandrahaar (moon necklace).
You are likely to find the process of distinguishing Bengali sarees from other sarees to be challenging, unless you come from a traditional family that is quite conversant in the clothes and culture of west Bengal. It becomes even more difficult to distinguish the different types of Bengali sarees, such as a Jamdani, Korial, muslin, and so on, because they look very similar from a distance.
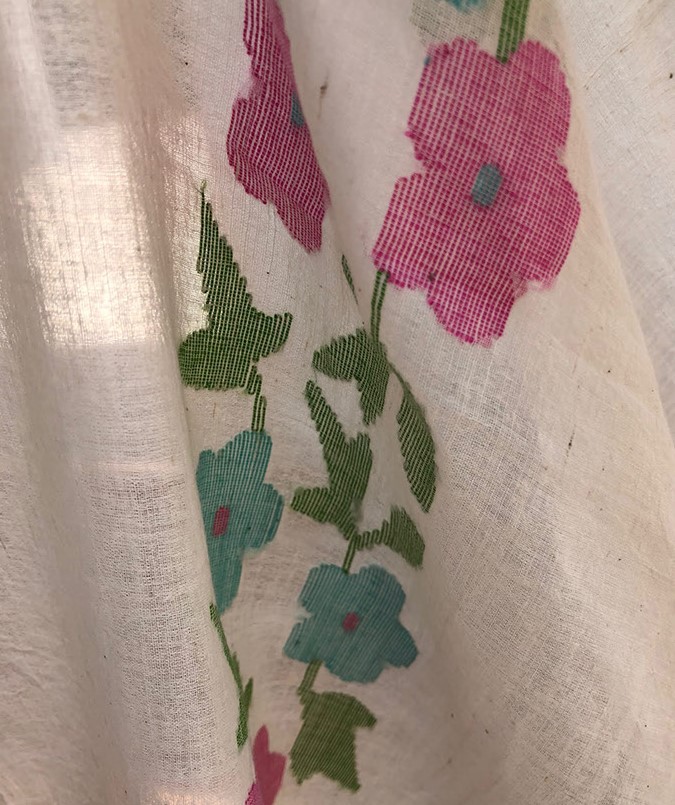
This makes it important to know the distinguishing aspects of each west Bengal saree, which are:
- Jamdani — these are lightweight sarees that are finely woven. They originally came in pure cotton, but now come in blends of silk and cotton to give them a glossy finish. Their motifs, interestingly, appear to float due to the fabric being almost transparent.
- Tant /Tangail — they have an airy and light texture due to the use of cotton as their main material. They are also suitable for everyday wear. They have a decorative pallu, thick border, and a plain body, and feature artistic motifs such as paisley and floral patterns.
- Muslin — these are ultra-fine sarees, which come in a sheer fabric, and have a shiny texture. The motifs are woven in a similar way to a Jamdani saree, but they are also quite expensive because of the weaving process, which is quite laborious and needs highly skilled workers.
- Baluchari — this is among the most beautiful Bengali saree types. The pallu and borders are very elaborate, and the weavings show various religious texts and historical epics. In addition, the weaving is done in colours that contrast the base colour of the saree. Interestingly, the most popular colours that are used for these sarees are purple and red. Along with Tant sarees, they also have quite bright colours, which make them stand out easily.
- Garad — are sarees made from pure silk, and have an off-white or plain white body along with a striped pallu and a simple red border (though the border can also come in other colours).
- Korial — this is considered to be a grander version of the Garad saree, as its silky texture is richer and the motifs are more intricate and ornamental.
- Tussar — the silk itself has a gold sheen, and the sarees will usually be in shades of honey, cream, tawny or beige, and can go through dyeing to attain brighter colours. The borders are very decorative, while the pallu motifs look similar to those of Jamdani and Tant sarees.
- Murshidabad silk — the silk is very high quality and lightweight, making them popular as casual and formal wear.
Jamdani is an enduring craft; its specialism lies in the ability to integrate new techniques. From contrasting monotones of white-on-white, its palette has expanded into colourful, vibrant forms. While Jamdani began as cotton muslin, its weaves have incorporated threads of silk, silver, gold and more to create fascinating iterations. Today, Jamdani is done on various materials, without involving machinery.
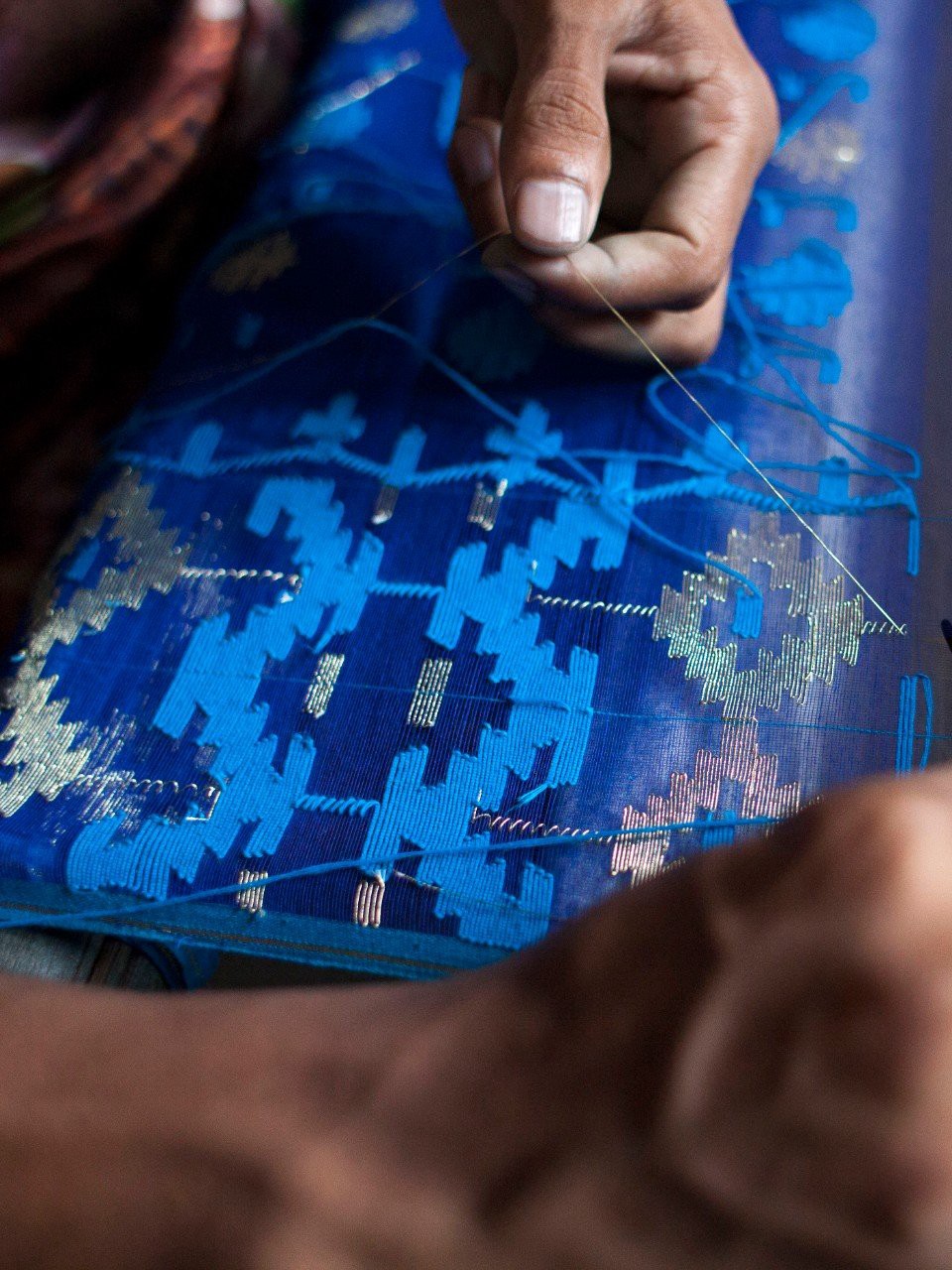
This art has travelled far beyond its birthplace — Dhaka, Bangladesh (erstwhile undivided Bengal). We can find the finest Jamdani weavers in Andhra Pradesh, Maharashtra, Rajasthan and Uttar Pradesh. The technique has gained unique features; it’s an art that displays an amazing variety.
It is a national heritage and preserving the national heritage is a responsibility. The Indian Jamdani weave form has enormous potential to make our traditional fabrics and design gain global appeal. The weavers in recent years have discovered that it is the only weaving technique with a sustainability factor. They have also found that this technique has given them enormous scope to bring about artisanal diversity.
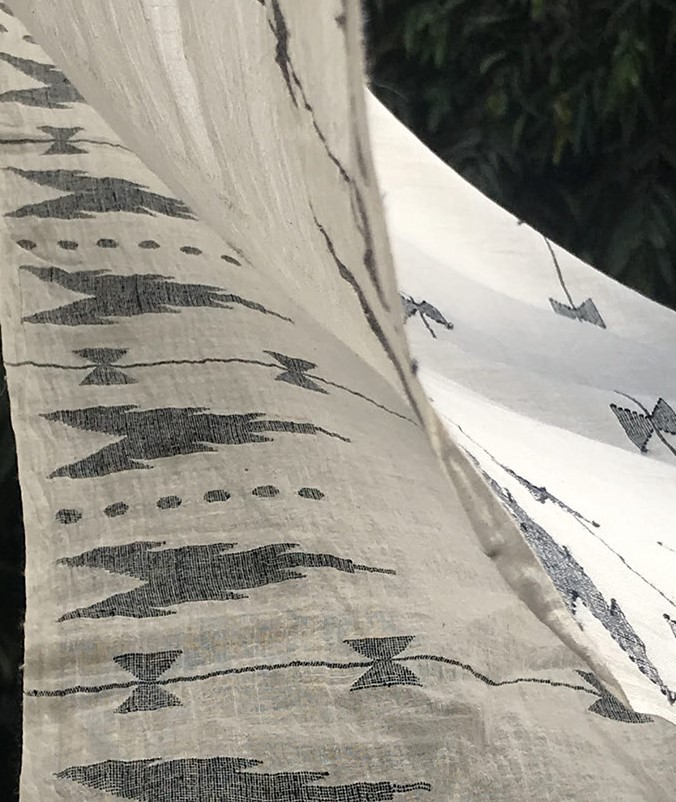
The handlooms have always enjoyed the prominent place in the fashion world as the most enduring, comforting and body friendly fabrics. As we move into an age of eco-friendliness, it has become even more relevant to preserve these ancient traditions that have eco infused in every step.
On a Jamdani weave, the word ‘contemporary’ takes many meanings. Sometimes, it means a revival of lost motifs and patterns. Sometimes, it means finding new inspirations.
There have been many variations engraved in the Indian Jamdani weaving technique, including gentle alterations of technique, the subtlest changes in yarn or number of threads, the most elusive hint of a new colour, and this weave continues to surprise handloom connoisseurs for its distinctive royal appeal coupled with the diversity of pattern and texture.
Modernising the weave combines inventing designs, motifs, colours and textures. The beauty springs from keeping the identity/ technique of the cluster and juxtaposing it with sensibilities that resonate with the present times.
The biggest test the sector faces is to develop continuous, constant skilling of weavers at the village level by master weavers and supervisors. As part of the social contribution, we have introduced a lot of programs to upgrade the skills of weavers, enrich their looms, and help them adapt to newer design approaches and bring about artisanal diversity, resulting in work for the weavers throughout the year.
Going forward, we believe that if the next generation isn’t enthused by handloom business prospects and the capabilities of Indian Jamdani weaving, we will be left with a handful of weavers. Fortunately, the fact is that there is a change, and there is a new sense of revival as a new generation of weavers carry forward the art within the weaver family.
Visual inspiration: the charm of Jamdani Weaving was originally published in UX Collective on Medium, where people are continuing the conversation by highlighting and responding to this story.